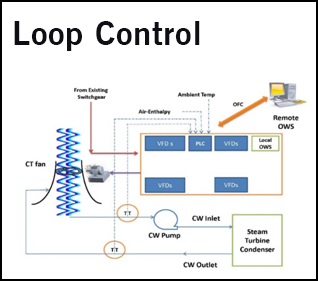
INTRODUCTION
Part load operation has introduced regime of auxiliaries unable to run at their best efficiency/design operating point. Power plant by design itself has numbers of flow regulating devices such as valves, damper, guide vane to meet varying process requirement. Retrofitting Variable Frequency Drives (VFD) Facilitates speed regulation of induction motor thus variable speed operation of Fan/Pump to meet variable process requirement and thus enable migration from throttling mechanism. VFD retrofitting also facilitates smooth motor starting thereby less stress on the mechanical components which further helps in saving maintenance cost and increased availability. VFD retrofitting essentially involves catering motor reliability issues, matching control philosophy and space requirement. Retrofitting being the case, compel to refurbish the existing motor instead of usually higher frame size inverter duty motor for addressing the motor reliability issues i.e. thermal and dielectric stresses. This chapter describes retrofitting of VFDs in Cooling tower fan motors for close loop operation depending on unit load and ambient conditions.
SOLUTION BRIEF
VFD environment of fast rising repetitive voltage pulses is very challenging in terms of Di-electric and thermal stress to the motors (especially random wound LT motors) thus usually requires use of inverter duty motor, very often of higher frame size, posing space constraint, alignment and other related problems during retrofitting. In case of retrofitting in existing motors the insulation and thermal scheme needs to be reviewed and addressed to meet the requirement. Thermal stress in case of load like CT fan which follow square Torque-Speed characteristics, is not an issue as Cu Losses reduce much faster compare to the cooling effect reduction by motor fan. For insulation upgradation dual coated magnet wire with Nomex composite paper based insulating paper used